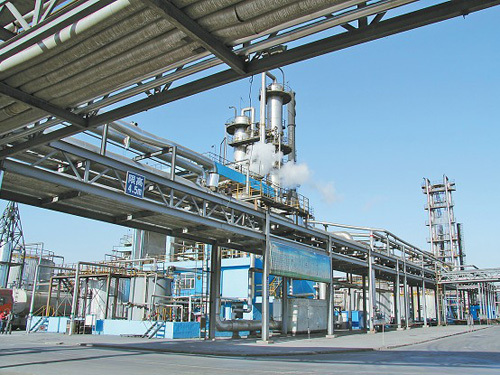
Character files Huang Hongning, born in Nanhai County, Guangdong Province in 1915, graduated from the Civil Engineering Department of National Sun Yat-sen University, Guangzhou in 1936, received a master's degree in chemical engineering from the University of Michigan in the United States in 1941, and a doctorate in chemical engineering from the University of Wisconsin in the United States in 1947. He has worked for many major chemical companies in the United States. After the founding of New China, Huang Hongning resolutely resigned from the work of earning a lot of money in foreign countries and made long journeys. He changed Britain, France, Belgium, Germany, Italy and other countries and returned to the embrace of the motherland at the end of 1951 and devoted himself to the chemical industry in New China. Huang Hongning participated in the whole process of the development of the nitrogen fertilizer industry in New China and presided over the introduction of many large-scale chemical projects, making important contributions to the development of China's chemical industry. He served as the chief engineer of the Nitrogen Fertilizer Design Institute of the Ministry of Chemical Industry, the deputy chief engineer of the Chemical Design Institute, the Planning and Design Institute of the Ministry of Petroleum and Chemical Industry, the chief engineer of the Planning Department of the Ministry of Chemical Industry, and the deputy chief engineer of the Ministry of Chemical Industry. He is the fifth national representative of the country and the sixth member of the National Committee of the Chinese People's Political Consultative Conference. He has been awarded the title of National Design Master.
Modern coal chemical industry is a very popular vocabulary in the current chemical and energy industry. In the current development process of the “Twelfth Five-Year Plan†in various localities, the domestic coal-rich regions and large-scale energy companies have competed to invest in the construction of modern coal chemical projects, and a large number of local projects have taken the initiative. According to incomplete statistics, in the case of coal to olefins projects, the domestic production capacity for construction contracts signed has reached more than 6.6 million tons, and new production capacity will reach 8 million to 10 million tons within three to five years; on coal-to-ethylene glycol projects Only a certain company in Henan plans to launch four projects with a capacity of 800,000 tons. Recently, with regard to the superiority of coal chemical products over petrochemical products, the coal chemical industry will replace petrochemicals. In this regard, a senior domestic chemical expert is deeply worried that he is the former deputy chief engineer of the Ministry of Chemical Industry Huang Hongning. The reporter recently interviewed Huang Lao.
The worst output of coal-based natural gas Reporter: This year is the first year of the “Twelfth Five-Year Planâ€. After the successful implementation of the large-scale national demonstration project, the development plan of modern coal chemical industry has been introduced in various places. As a senior coal chemical expert, what do you think about the development of modern coal chemical industry during the 12th Five-Year Plan period?
Huang Hongning: During the "Eleventh Five-Year Plan" period, due to the high international oil prices, China's coal chemical industry with its raw material advantage has developed rapidly. In order to avoid investment risks, the National Development and Reform Commission has deployed five demonstration projects of modern coal-based chemical industry: coal-to-oil, coal-to-olefin, coal-to-ethylene glycol, coal-to-dimethyl ether, and coal-to-natural gas. At present, with the exception of coal-based natural gas, these modern coal chemical demonstration projects have all been successfully built, making the domestic coal-rich regions and large-scale energy companies plan to build modern coal chemical projects one after another. There are also problems with blind development and lack of scientific planning. I can say that I was engaged in coal chemical industry for the rest of my life and I am very concerned about the current development trend of coal chemical industry in China. I have collected and sorted out the information of modern coal chemical projects that have been started, and analyzed them with three indicators, namely the equivalent raw material output efficiency, investment output ratio, and resource utilization efficiency.
First look at the unit of raw material output efficiency. The same amount of 4,000 cubic meters of coal-syngas or 2.5 tons of high-quality anthracite is used as raw materials to produce coal-based natural gas, indirect coal-to-liquid, direct-coal-to-oil, coal-to-olefin, coal-to-dimethyl ether, and coal. The respective output benefits of ethylene glycol are 2000 yuan, 4510 yuan, 4687 yuan, 4703 yuan, 4948 yuan and 6700 yuan.
The second is to look at the ratio of investment to output. Assuming that coal-to-natural gas, indirect coal-to-oil, direct-coal-to-oil, coal-to-olefin, coal-to-dimethyl ether, and coal-to-ethylene glycol projects will be driven at full capacity throughout the year, based on current prices, one-year investment-output ratio It is 0.388, 0.487, 0.527, 0.26, 0.667, and 0.69.
The third is from the perspective of the utilization efficiency of coal resources. Coal-to-olefins produce 1.5 tons of water per ton of olefins produced, indirect coal-to-oil produces 1.2 tons of water for every ton of oil produced, and 0.4 tons of water per metric ton of dimethyl ether produced from coal. This all reduces the energy efficiency.
Judging from these major economic indicators, these coal chemical projects vary. Among them, the raw material output efficiency of coal-based natural gas is the worst. This is because the degree of deep processing is low and the added value of products is too small. The investment-to-output ratio of coal-to-olefin production is the worst, indicating that the investment needed for the project is too large. Therefore, we must invest prudently in coal-to-natural gas and coal-to-olefin projects.
Domestic projects are too admiring for foreign technology reporters: What do you think is the main reason why some domestic modern coal chemical projects have low investment returns and low energy utilization rates?
Huang Hongning: First, due to its own technical limitations. The synthesis of these modern coal chemical products can not be separated from two major elements - carbon and hydrogen. The hydrogen content of coal is much less than that of petroleum. Therefore, coal chemical industry must produce hydrogen from coal, sometimes hydrogen becomes water in vain and consumes more energy than oil. The development of modern coal chemical technology is relatively late and many fields have yet to be developed. At present, coal-to-olefin technology is being developed for the use of four-carbon technology, with a ton of olefins and methanol consumed from 3 tons to 2.67 tons. However, this needs to be further developed. The direct synthesis of olefins from syngas is an endeavor direction, and its R&D work should speed up the pace and produce early results.
Second, some modern coal chemical projects in China are too advocating foreign technology, and many are introduced and costly. For example, the coal-to-olefins project of Shenhua Group, except for the conversion of methanol to olefins, is a domestic technology, and other processes adopt a large number of imported technology and equipment: 7 gasifiers are based on GM's 1,500 tons per day. Coal-water slurry gasifier; two syngas purification units of 265,000 m3/h, using low-temperature methanol wash process of Linde GmbH of Germany; 1.8 million-ton/year methanol plant, using British David's Low-pressure methanol synthesis technology; 300,000-ton/year ethylene and 300,000-ton/year propylene olefin separation/purification unit, designed by Lummus Corporation of the United States; its polyethylene and polypropylene units are also introduced. Another large-scale coal-to-olefins project that has been completed in China has its technology and equipment imported.
In fact, modern coal chemical syngas, low-temperature methanol wash, methanol low pressure synthesis and other technologies, the domestic chemical industry has long been mature technology; olefin separation, ethylene and propylene polymerization and other processes, the domestic petrochemical industry also has domestic technology. Our domestic technology level is not bad and investment can be reduced. I have done a program comparison for a certain coal-based natural gas project, such as the localization technology of brown coal pulverized coal pressurized gasification, and first extract the comprehensive utilization of volatile coal, the cost per cubic meter of natural gas can be achieved 1.06 yuan; with domestic The coal-water slurry gasifier has a cost of 1.6 yuan per cubic meter of natural gas. With shell gasification, the cost per cubic meter of natural gas is 2.16 yuan.
The carbon emissions of modern projects are inferior to those of traditional reporters: Some reports reflect that the carbon emissions from modern coal chemical projects are too high. What do you think?
Huang Hongning: Indeed, some very hot modern coal chemical projects have high carbon emissions. Carbon emissions are actually the loss of coal. High carbon emissions will inevitably lead to high energy consumption. High energy consumption will inevitably lead to poor economic returns. For example, indirect coal-to-oil production requires more than 2 tons of carbon dioxide for each ton of oil produced, and every ton of dimethyl ether produced for coal produces two tons of carbon dioxide. The carbon dioxide product produced by the project itself cannot be used, so the economy is also very low, and it does not even reach the level of some old traditional coal chemical projects. For example, the coal-to-urea project of the traditional coal chemical industry has an investment-to-output ratio of 0.64, and the output efficiency per 4,000 cubic meters of syngas can reach 5,975 yuan. This is higher than indirect coal-to-oil, coal-to-natural gas, coal-to-olefin projects and coal-to-dimethyl ether. From the perspective of low carbon requirements, urea production is not behind now. After years of development, the coal-based urea technology is improving day by day, and energy in production will not become water. The process itself can partially utilize the carbon dioxide emitted. The urea produced by natural gas can be used up as carbon dioxide emitted by itself, and it can also absorb carbon dioxide outside the system. Natural gas urea can be said to be the most advantageous raw material route at present, which combines the advantages of low-carbon, environmental protection, energy saving and low cost. As the most populous country in the world, food security is a top priority that China has always ensured. Petrochemical companies should do their utmost to produce some natural gas to develop urea projects.
Reporter: The coal-to-oil project is divided into direct coal-to-petroleum and indirect-coal-to-coal, both of which have built demonstration projects in China and are put into production. Which technology is more advantageous now?
Huang Hongning: From the actual operation of the demonstration project, it can be found that the direct coal-to-oil projects are more economical than the indirect coal-to-oil projects. This is due to the Fischer-Tropsch reaction of indirect coal-to-coal oil production, which requires 1.2 tons of water for each ton of oil produced, resulting in higher energy consumption. Therefore, I think that during the “12th Five-Year Plan†period, it is necessary to make a good industrial layout for indirect coal-to-oil projects and choose cheap raw coal and appropriate technical equipment. Otherwise, such projects lack market competitiveness.
Shenhua's direct coal-to-oil technology has independent intellectual property rights. It produces no oil at the same time and has a high energy utilization rate. However, the device still has the problem of not being able to operate stably for a long period of time. It is understood that this device does not have a main pump heat exchanger, which may be one of the causes of the failure. According to foreign reports, the main pump of the reactor, which is prone to failure, is sealed. When necessary, the design of product oil packing can be adopted. At present, the liquefied oil slag of the device is directly used as boiler fuel. If the oil residue extraction device is on, the coal consumption can be further reduced. It is expected that during the “12th Five-Year Plan†period, the domestic supply of refined oil, especially diesel, is not optimistic. It is necessary to properly develop coal-to-oil projects.
The petroleum route is not worse than the coal route. Reporter: When experts analyze the economics of modern coal chemical industry and petrochemical industry, they believe that modern coal chemical industry has significant economic performance. For example, 3 tons of methanol on the coal route can produce 1 ton of olefins, and 3 tons of naphtha on the oil route can make 1 ton of olefins. The naphtha is more than 3 times more expensive than methanol. Therefore, the efficiency of coal to olefins is good. How did you see this problem?
Huang Hongning: There are quite a few conclusions about the effectiveness of modern coal chemical projects than petrochemical projects are biased. The example you are talking about, and careful analysis shows that he used the internal coal pit price when calculating the methanol price, and used the market commodity price when calculating the naphtha price. In fact, naphtha is also an internal product of petrochemical companies. If the company’s internal price is considered, it is also very low. Also, olefins should be considered ethylene, propylene, and butadiene, which are all high-value products. Now that petrochemical companies improve their technology and increase their yields, they typically produce 1 ton of naphtha out of 1 ton of triene. The remaining 1 ton of products are methane, hydrogen, pyrolysis gasoline, liquefied gas, and fuel oil. Petrochemical enterprises can be eaten dry, comprehensive utilization, and high returns. The 3 ton of methanol produced from coal to olefins produces 1 ton of olefins. The remaining 2 ton of product has more than 75% of water, only 3% of methane hydrocarbons, 1% of ethane gas and 3.7% of liquefied gas. The value is very low. Therefore, if the comprehensive utilization of product value is considered, olefins produced by petroleum cracking will not be inferior to coal-based olefins.
Reporter: In your opinion, how should you resolve the contradiction between the oil route and the coal route?
Huang Hongning: To develop China's ethylene industry, we should not separate petrochemicals and coalification, and we should advocate the integration and win-win development of the two industries. Ethylene and propylene are just raw materials and olefins have only opened up. Downstream deep processing of olefins is still a technology-intensive industry with huge investments. After decades of efforts, the domestic petrochemical industry has developed a considerable foundation in this regard, and the coal chemical industry has no need to spend money to start another stove. The downstream processing of modern coal chemical companies is concentrated on a few products such as polyethylene and polypropylene, but they do not know that these products have long been overcapacity by the petrochemical industry. Instead of seriously overcapacity of certain olefin products in the petrochemical industry, it is also necessary to blindly develop the production capacity of these olefin products from coal raw materials.
In addition, the domestic petrochemical industry should also learn from methanol to olefin technology. The catalytic cracking unit of a refinery company can easily be converted into a methanol to olefin plant, and a large amount of refinery dry gas, ethylene cracking tail gas, methane hydrocarbons, and hydrogen generated during production are good raw materials for methanol and olefins production. It is understood that domestic Maoming, Dalian, Jinxi and other petrochemical enterprises have spare catalytic cracking idle devices. Using these devices to make methanol to olefins can get a multiplier effect. At the same time, petrochemical companies should also cooperate with coal chemical companies to use the existing olefin deep processing technology and equipment in the petrochemical industry to develop deep processing of coal-to-olefin feedstocks, avoiding repeated investment and repeated construction by the state.
Petrochemical deep processing should be included in the national strategy reporter: There is an argument that coal chemical industry should completely replace petrochemicals. How do you evaluate this?
Huang Hongning: At a time when global oil supply continues to increase at this stage, it cannot be said that when coal chemical industry has completely replaced petrochemicals, it can only be said that coal chemical industry is a supplement and a technical reserve for petrochemical industry. At present, many domestic economic analysis of modern coal chemical industry and petrochemical industry adopt the assumption that all international crude oil is imported, and the calculation is based on the international high oil price. In fact, China is also the fourth-largest oil producer in the world. Half of the country's oil production is produced by petrochemical companies. There is a huge profit margin for the cost of oil produced by us compared with international oil prices. Contrary to what they say, petrochemicals are not as good as coal chemical industry. Several major petrochemical enterprises in China are still profitable and are the pillars of national fiscal revenue. Therefore, they have inconsistent calculation methods and do not count the benefits of comprehensive utilization by petrochemical companies. Therefore, it is incomparable and incorrect.
The petrochemical industry is still a sunrise industry and will not be overshadowed by the rise of the modern coal chemical industry. In the past half century, petrochemical technology and industry have achieved rapid development. Whether domestic or foreign, petrochemicals are irreplaceable regardless of technology, advanced quality or industrial economy. The “Twelfth Five-Year Plan†for petrochemical development should make great efforts to promote deep processing, produce high-end products, and strive to improve the production technology level of China's petrochemical and chemical products. To promote the integration of petrochemical industry and coal chemical industry, and to coordinate development, it is crucial for China to reduce the dependence of chemical products on foreign markets and safeguard the supply of refined oil products. Therefore, I suggest adding petrochemical deep processing to the list of national strategic emerging industries to play a role in the development of China's new materials and new energy industries.
100W Flexible Solar Panel,Semi Flexible Panel,Flexible Pv Mudule,Waterproof 100W Flexible Solar Panel